By Kathleen Maynard, Senior Director, Building Innovation, CHBA
Canada faces critical, simultaneous challenges – housing supply and affordability, and the effects of climate change. Innovation and action to increase productivity, lower greenhouse gas (GHG) emissions, cut costs and enhance resiliency are essential to meeting these challenges. Research, demonstration and practice to date shows that modular construction is part of the solution.
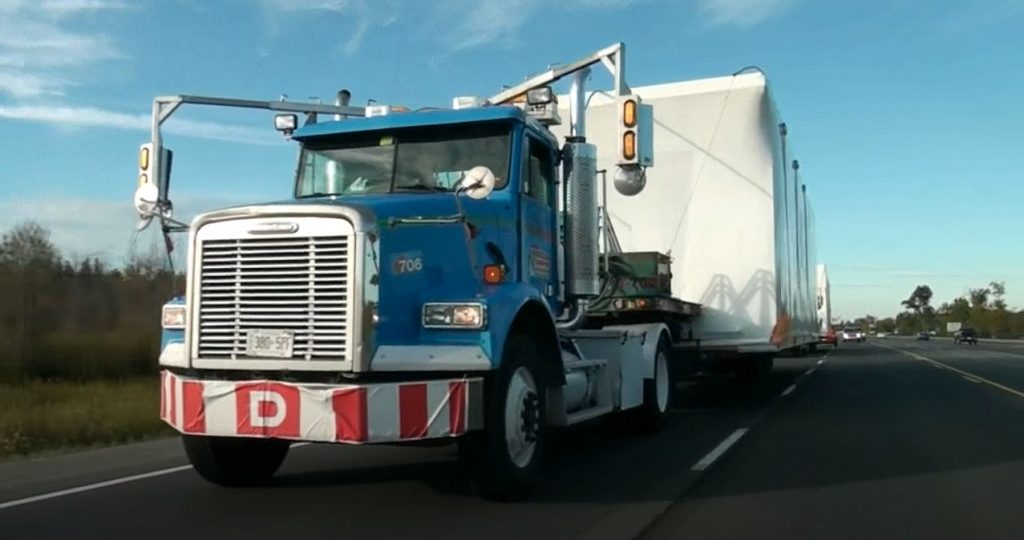
Focus on productivity
With 22 per cent of the labour force set to retire, Canada will need 128,000 new workers in residential construction over the next decade. With every sector of the economy short on workers, all sectors will be competing for the same insufficient pool of people. Despite all efforts to attract and train the future workforce, and even though Canada is increasing immigration and targeting construction workers (which is good), Canada also needs to double housing starts, meaning that there will almost certainly still be a labour shortage. We’ll need to build more houses with fewer people. Innovation to improve productivity on-site, and especially to increase capacity and adoption of factory-built systems, will be important to meeting our housing supply and affordability needs. A 2019 McKinsey report, Modular Construction: From Projects to Products, found that modular construction can speed construction by up to 50 per cent, and lower costs by 20 per cent. While increased automation offers further productivity improvements both in the factory and on-site, there will be a need for new skills in design, manufacturing operations and digital technologies.
Action on climate change
Increased innovation and capacity in factory- built systems will also help meet the challenge of climate change. CHBA’s Modular Construction Council members were among the pioneers of energy-efficient construction, and they continue to lead the way with net zero. While energy-efficiency has long been the surrogate for GHG emissions reduction – and continues to be a critical measure, especially in relation to the existing housing stock – environmental knowledge and building practices are evolving beyond operational emissions to embodied carbon, in both materials and processes. A University of Alberta comparison of modular and on-site construction, documented in the North Ridge CO2 Analysis Report, found that modular construction processes resulted in a 43-percent reduction in GHG emissions versus building solely on-site. Modular construction processes also result in significantly lower rates of materials waste, which not only reduces embodied carbon rates in materials, but also reduces materials (and associated logistics) costs. The McKinsey report found that the savings in materials waste in building factories alone could lead to a 10-per-cent reduction in costs.
Beyond climate change mitigation, the homebuilding industry continues to innovate, and builders are incorporating modular solutions to build homes that also address adaptation and resilience to accommodate changes in climate and withstand and recover from extreme climate-related events.
In relation to extreme climate risks – overheating, flooding, rain/hail resistance, tornado resistance and wildfire resilience – for the most part, finished homes can offer the same level of protection whether factory or site-built. However, factory-built homes generally offer higher wind resistance against lateral loads and uplift forces because they are built to resist higher winds for transportation.
The environmental advantage
- Highly energy-efficient homes and buildings due to indoor construction conditions, integrity of a continuous air barrier and insulation layer and careful sealing
- Optimized materials use and minimized waste production due to precision production processes, reuse and recycling, and protection from weather damage and vandalism
- Reduced CO2 emissions during construction factoring material delivery trips, crew trips, equipment usage and winter heating
- Efficient development opportunities such as small-lot community design; community energy systems; surface foundations; infill; garden suite, laneway housing and tiny homes
- Increased protection from overheating or during a flood, rain/hail, tornado or wildfire event, and faster rebuilding afterward
This means that in locations where such high levels of resistance are not required, factory-constructed homes would most likely fare better at the site during a tornado event than code-compliant homes built on-site.
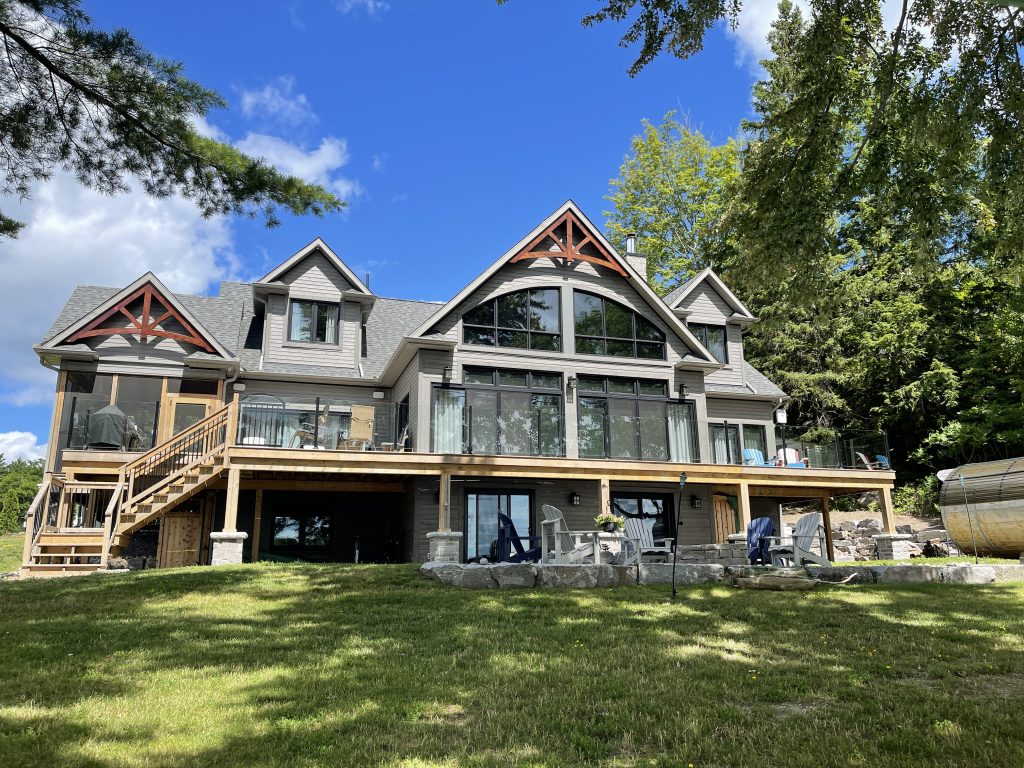
When it comes to resilience during construction, however, modular construction offers distinct advantages. In relation to overheating, while a home is being constructed, the site-built process can offer passive protection like shading or active protection with A/C equipment, based on the construction stage. In the factory, people and materials are usually in a conditioned environment and protected from direct sunlight.
If a flood occurs during construction on-site, there may be damage to a partially built home. In the factory, the home will not suffer any damage (assuming of course that the factory is not affected by the same flood).
During rain and hailstorms, tornadoes and wildfire events, it is quite possible that a home or building under construction could be exposed to forces or elements that a half-completed roof, structure or cladding cannot withstand. During these extreme events, it is difficult to protect site-built projects that are under construction.
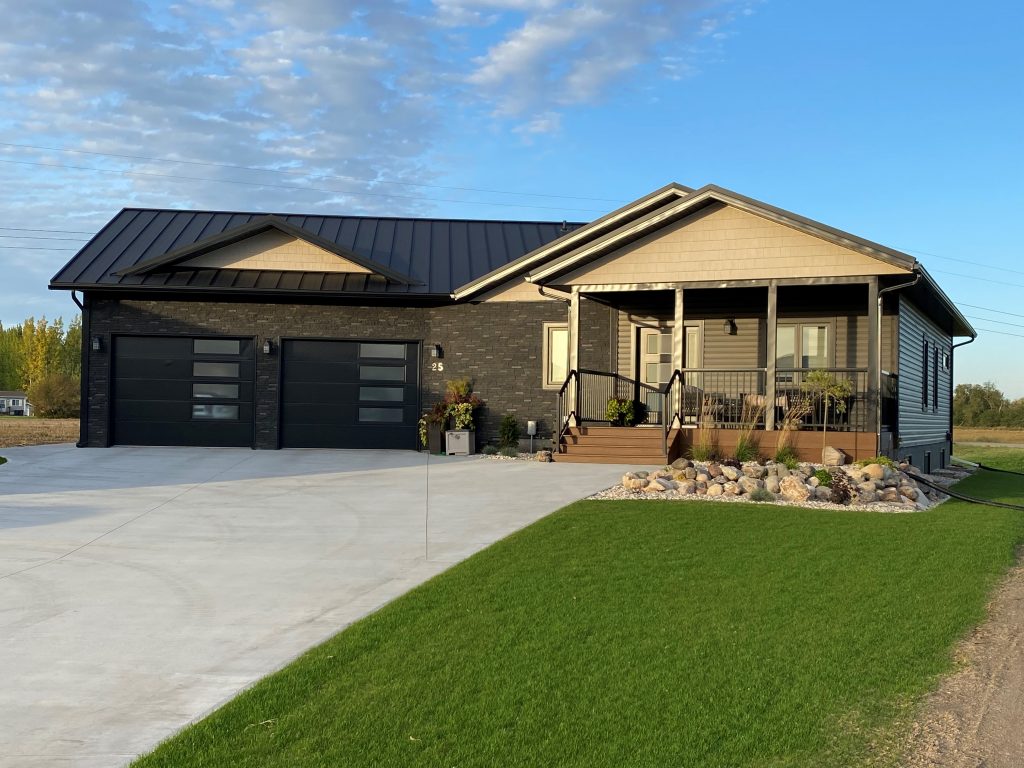
In the case of a wildfire, it may not even be a wildfire on the project site, but a wildfire 25 km away, for example, that could stop the construction activity for insurance purposes. In all these cases, the factory-based construction process has a clear advantage. Construction of the superstructure can take place during a climate event – assemblies will not be destroyed by being exposed to the elements or extreme forces, materials will not be compromised by fire or water, and structural connections will not be loosened by wind. In addition, community recovery is faster when rebuilding can take place offsite in a location that was spared from the extreme event.
For all these reasons, CHBA’s Modular Construction Council continues to advance the field of factory-built construction in Canada. For information on modular construction, check out the CHBA Modular Construction Council’s “Working with Modular” webinar series at chba.ca/modular.