SPONSORED CONTENT
Building a better future in construction
Acting on climate change has become an international priority, and the heavy construction sector is among the biggest contributors to CO2 emissions worldwide. As Canada’s largest general contractor, PCL Construction is leveraging Milwaukee Tool’s battery-powered MX FUEL Equipment System on the Cascade Power Project to lessen environmental impact, improve safety and efficiency on the jobsite and reduce operating and maintenance costs.
Once commercial operations commence in 2023, this combined cycle power plant is expected to lead the transition from coal-fired power to clean electricity in Alberta.
“Our goal is to have the leading-edge technology to complete the project successfully and on schedule,” says Brian Waritsky, warehouse manager at PCL Construction. “With MX FUEL, we’re giving our tradespeople the ability to execute their work more effectively.”
Project profile
Project: Greenfield combined cycle 900 MW power plant
Location: 16 km south of Edson, Alta.
Jobsite size: 11 hectares (27 acres)
Approximate workforce: 1,080 people at peak
Construction started: September 2020
Total construction costs: C$1.3 billion
Fuelling innovation
As the construction sector searches for innovative ways to meet sustainable development goals, battery-powered technology provides one of the biggest opportunities to reduce harmful jobsite emissions that pose risks to end users and the environment.
“I’ve been on sites this size and larger where you can tell that the generators and compressors have been running all night, especially on those frigid Canadian winter mornings,” says Ken Hanley, general superintendent at PCL Construction. “Last winter, we didn’t experience that here.”
PCL Construction has been transitioning over to MX FUEL since discovering the system delivered reliability and durability for heavy use on industrial projects without the hassles and hazards associated with gas and pneumatic equipment.
The company’s largest investment has been in the MX FUEL ROCKET Tower Light/Charger with over two hundred units in their fleet. The tower light emits zero emissions, has a wheel-based design and weighs in at only 108 pounds, so moving it is a one-person job. For comparison, a diesel light tower requires refuelling, spill containment, and a forklift to place the unit because it weighs about 1,600 pounds.
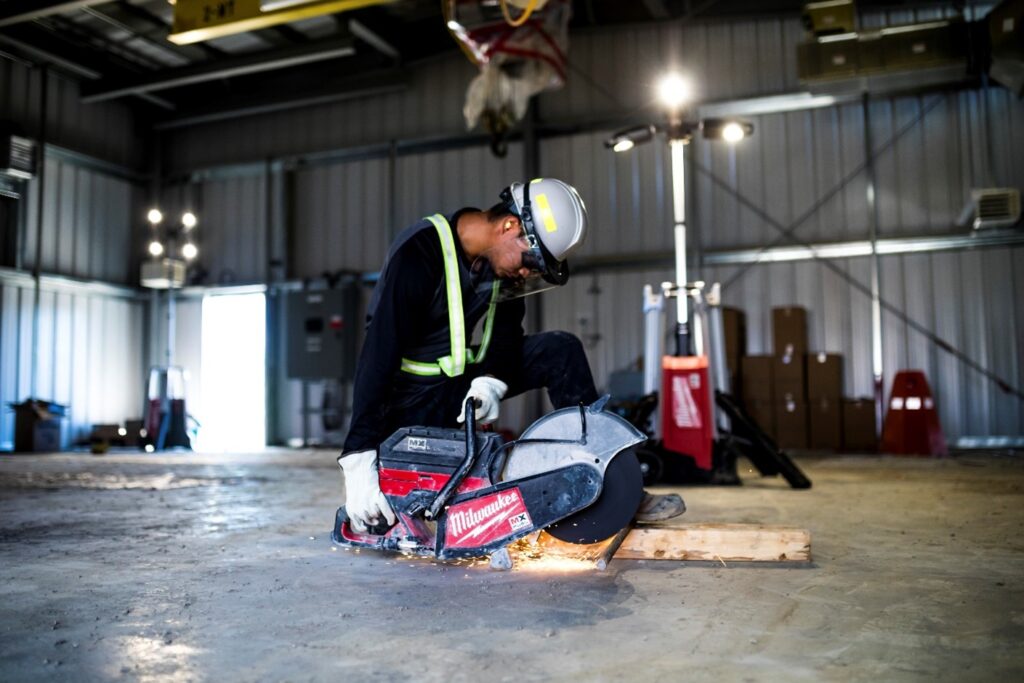
“When we ran the data from 2019 to June 2022, our estimated fuel burn for diesel-powered light towers was 250,000 litres over this time period,” says Scott Sharun, senior procurement and equipment manager with PCL Construction. “If we remove one diesel light tower for a winter, we reduce emissions by an estimated 9.6 tonnes of carbon output per diesel light tower. That’s a game changer.”
Improving safety and efficiency on the jobsite
The MX FUEL Equipment System eliminates exposure to the emissions, fumes and noise pollution of gas tools, especially when you factor in idling time. Battery-powered tools start with the press of a button and there’s no need for spill kits, spill trays and fire extinguishers.
“MX FUEL produces zero emissions inside buildings and eliminates the hazards associated with air lines and cords, both of which are huge safety improvements on our jobsites,” says Roger Keglowitsch, chief operating officer for heavy industrial at PCL Construction.
Since some builds are vertical, getting lighting and heavy gas-powered equipment onto higher floors can also be challenging. The lightweight and cordless MX FUEL™ Equipment System removes limitations on jobsites where mobility is critical.
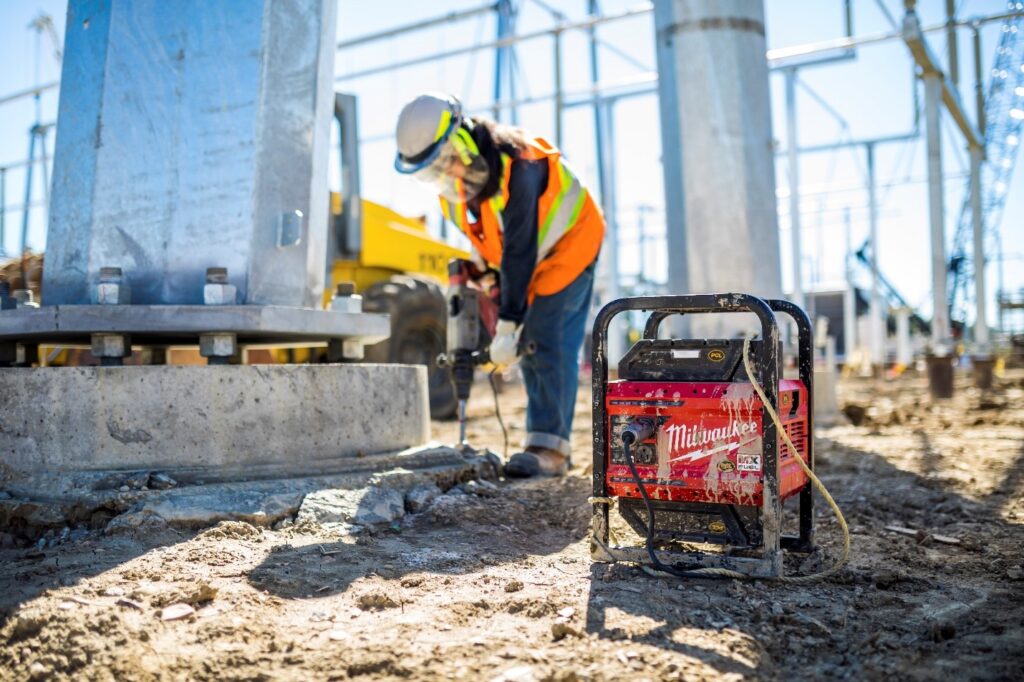
“Previously, your productivity only went to the end of an extension cord or to the elevation an air hose could reach,” says Waritsky. “MX FUEL allows our workers to be far more productive in more areas while mitigating safety concerns.”
Profitable sustainability
PCL Construction is 100-per-cent employee-owned, which drives accountability and engages every employee in the pursuit of more environmentally responsible construction practices. Transitioning to battery-powered tools has helped to reduce costs and waste, thereby aligning the company’s sustainability goals with financial performance.
Gas and pneumatic tools involve more moving parts, increasing the chances of damage and reducing the tool’s lifespan. On top of that, it’s hard to find field mechanics who can service and repair small gas engine units for sites operating 24 hours per day, seven days per week, and this impacts the site’s ability to stay operational and productive.
“We were replacing a lot of cords and parts with our older equipment,” says Sharun. “We’ve seen a significant reduction in service and labour costs with our MX FUEL fleet because there’s no risk of over-throttling, cords and hoses are gone, fouled plugs and burned-out mufflers are gone; and all the issues around fuel in winter on small combustion engines. Providing limited downtime and service requirements increases utilization as we aren’t waiting for parts or repairs.”
On top of that, because MX FUEL is ONE-KEY compatible, PCL Construction has been able to geo-fence a project site and easily track asset location to reduce loss by remotely disabling batteries when they wander off site.
Forward thinking and future ready
Every project in PCL Industrial in Canada has access to or is currently using MX FUEL. “We’re hungry for all the innovations that come with battery power,” says Sharun. “We want out of gas and diesel, and we want out of cords.”
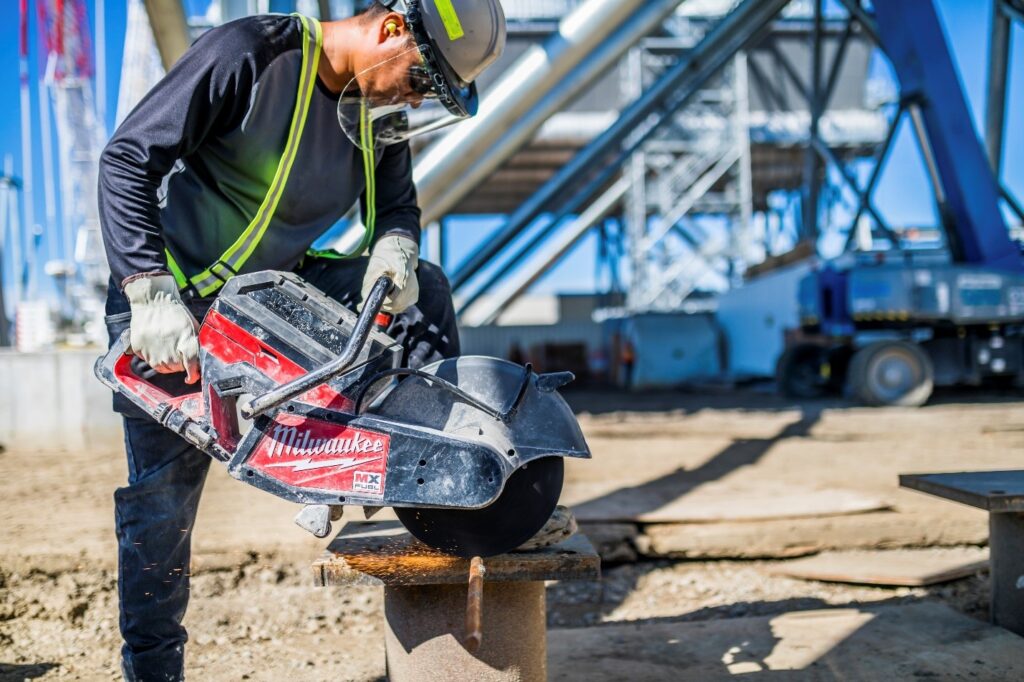
According to Sharun, the ability to quickly deploy MX FUEL results in an operating site by lunchtime. Meanwhile, those using gas are still unwrapping skids, running cords everywhere and trying to figure out where to put their fuel tanks.
Tradespeople are also getting harder to attract, Hanley adds, so it’s important to show that you’re evolving and using the latest and greatest gear. “MX FUEL has allowed us to do that,” he says. “We’re able to make the best technology available for them to do their job and that makes them want to work for our company.”
For more information about MX FUEL, visit milwaukeetool.ca/mxfuel.