By Natasha Rombough, Director, Marketing and Communications, CHBA
If there’s one challenge that has been constant for Canada’s residential construction industry in recent years, it’s reliable access to skilled tradespeople. And with baby boomers retiring – BuildForce Canada says we can expect 20 per cent of our labour force to retire, with 40 per cent reaching 55-plus, in the coming decade – the difficulties will only increase. Add in Canada’s housing shortage and the need to double housing starts over the next decade to somehow produce 5.8 million new homes, plus the federal government’s commitment to achieving net-zero emissions by 2050 (which will require extensive renovations of existing homes), and the situation is unmanageable.
Immigration has a role to play in augmenting the industry, and it will take smart immigration policies to make sure labour shortages in residential construction are addressed. Our industry offers a pathway to successful careers for immigrants, but we need to target the right entrants with the right competencies, transferrable experience, and desire to build a career in the industry. During CHBA’s Day on the Hill in May 2023, Housing Minister Sean Fraser spoke of changes coming to Canada’s immigration, which will be an important change for the sector, and CHBA is seeking still more improvements to help ensure we get the workers we need.
But the reality is that Canada will be hard-pressed to make up the skilled trades gap, even with improved immigration. What we need is an industry transition that approaches homebuilding in ways that allows our sector to become more productive. The solution to improved productivity is factory-built construction, including panelization and modular construction – this is not a new concept, but to get there will require new and innovative supportive government policy.
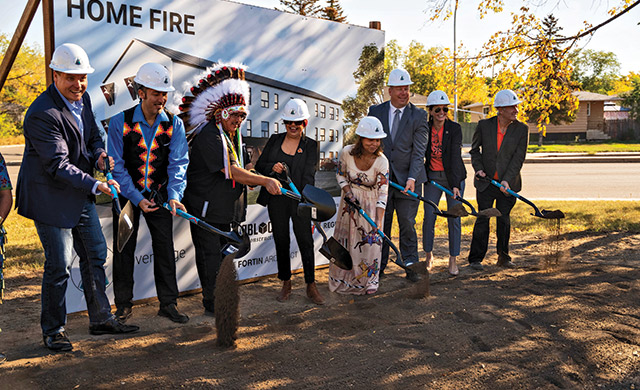
Factory-built solutions
In modular construction, the home is built in one or more three-dimensional modules in a factory and then shipped to the site. Panelized systems – where two-dimensional wall and floor panels are pre-built in factories and shipped to site – are also an option for making use of factory-built construction. Both approaches can be used for small homes to large homes to multi-family buildings. Factory construction offers many benefits and opportunities. It’s more efficient from a time and material perspective, which gives it an edge over on-site construction. It’s also shown to create less greenhouse gas emissions and construction waste.
According to CHBA’s Housing Market Index (HMI), nearly 30 per cent of respondents used some form of factory-built components (such as modules and wall panels) in the last year, and 90 per cent are considering using them in the next one to three years. Clearly, builders are seeing the advantages of the reduction in on-site construction time and reduced labour requirements. We need to lean into adopting more factory-built solutions, but there are challenges to overcome to do so.
Top benefits of factory-built construction
• Faster construction with fewer delays
• Year-round work with limited weather issues
• More energy efficient and less waste
• Increased output with less labour
• Easier to get labour (fewer barriers to entry, appealing conditions, good for immigration, including temporary foreign workers)
Factory-built challenges
There are already many modular housing and panelization factories across the country, but to transition the industry to making more use of the solutions and the added productivity they offer, we’ll need to make use of and expand the capacity of existing factories and add more factories moving forward. That’s easier said than done.
The ebbs and flows of demand for housing can impact companies’ ability to sustain the necessary throughput to warrant factory development and/or expansion. There is a substantial capital cost investment required to set up a factory, with high overhead, and even more to maximize productivity through advanced automation, which means there can be substantial risk in market slowdowns. Factories require a steady workforce and consistent demand/throughput, and carry high overhead, which makes them not as flexible during boom-bust cycles as site-built construction. Some financial institutions still aren’t well-versed in financing flexibility for the modular construction process, and there are other systemic barriers as well.
Transitioning the sector
CHBA’s Sector Transition Strategy provides the government with concrete steps it can take to help to address Canada’s housing crisis and improve housing affordability through the increased productivity of factory-built solutions. The Strategy was developed with input and feedback from members from across the country via CHBA’s national committees and councils. CHBA’s Modular Construction Council, which is made up of representatives from many of Canada’s current factories, outlined key elements for this transition of the sector during a strategic planning session in the spring of 2023, including identifying many of the benefits and barriers to such a transition. The Strategy was further refined at CHBA’s fall meetings. Since then, CHBA has presented it extensively to government officials, including in discussions with Sean Fraser, the federal minister for housing.
The Strategy outlines four needed systemic changes: Change to the financial system to enable Canadians to buy their first homes and to enable investment in purpose-built rental, both in turn enabling more housing starts; change to policies that allow for fast-tracking of development and lower construction costs; change to the labour system to provide enough workers; and change to productivity, which will require substantial capital investment that must be incented and de-risked. This latter section on productivity is elaborated on extensively, offering concrete recommendations for government policy and programming to see it come to fruition.
The fact of the matter is that to increase productivity to increase housing supply and affordability, which is the core of the transition strategy, the government needs to support investment in factory-built construction with the same urgency and approach as they are focusing on Canada’s clean economy plan. CHBA’s Strategy explains how.
Example of success: Rapid housing project in Regina
A great example of modular productivity is the construction of Horse Dance Lodge in Regina. The three-story, 29-unit assisted-living residential building was completed by CHBA members Big Block Construction and modular factory Grandeur Housing, along with many other collaborators, including project owners Silver Sage Housing Corp., which provide and promote high-quality social housing for First Nations people living in the Regina area.
The project was part of Canada Mortgage and Housing Corporation’s (CMHC’s) Rapid Housing Initiative (RHI). Launched in 2020, the RHI provides finding to facilitate the rapid construction of new housing and the acquisition of existing buildings for the purpose of rehabilitation or conversion to permanent affordable housing units.
Horse Dance Lodge was successfully completed on time and on budget, going from foundation to handover in five months. Big Block and Grandeur Housing have been working together for more than 10 years and have honed a great working rhythm. CEO Alex Miller says he hopes that learnings from successful RHI projects are unpacked so that they can be scaled and applied across the country. “If we take less of a shotgun approach to these projects and instead make sure that we dive in and scale the elements that are working, that’s what’s going to help solve the housing shortage problem,” Miller says.
The project wasn’t without its challenges, though. To meet project construction timelines, the modules were craned into place on April 12 and 13, 2023. But some approvals were only confirmed on March 28. How was that possible? Risk. To ensure the project was complete on time and on budget, construction in the factory was started before all items were finalized, which caused a lot of added stress in addition to risk. It took 142 days to build the entire 20,000-sq.-ft. structure in a factory. It took longer just to review and approve the permits.
“Sharing risk is one thing,” says Miller, “but taking unnecessary risk is something we all have to pay attention to because it’s critical to all housing projects.” Miller sees the systemic problems within the residential construction industry as opportunities to improve and get more houses built faster and more cost-effectively. “This project was craned into place in one-and-a-half days. Our current single craning crew can crane 5000 units a year. Imagine if we could solve some of the systemic problems? We have the answer to the housing shortage right in front of us.”
The Rapid Housing case study of Horse Dance Lodge was the subject of a recent webinar in CHBA’s “Working with Modular” webinar series. You can watch the webinar at chba.ca/modular#modular-series.